Binding of multi-section books has long been one of the most complex post-press finishing tasks, and digital print brings both benefits and challenges. Simon Eccles looks at the current state of the art
Book binding history started with thread sewing in pre-Gutenberg days, with the first glue-based ‘perfect binders’ appearing about a century ago. Both venerable techniques have been adapted for the challenges of digital printing, where pre-collation of pages is a benefit but short runs of variable size and thickness is a considerable challenge.
In volume production by full-time specialists, the printers for book blocks are now almost always high speed web-fed inkjets. However, smaller scale production is well within the range of many service providers with sheet-fed digital presses. It doesn’t matter much for the binding process, as the paper always has to be cut into sheets at some point. Roll-fed methods need different feeders and possibly sheet cutters in the line, though the potential volume determines the configuration of the actual folding and binding systems.
Muller Martini from Switzerland was really the first to recognise digital as a potential new market, having introduced its first SigmaLine system for binding digitally printed books at drupa 2000. Today’s SigmaLine systems can be configured for web widths up to 1066mm, as handled by the HP PageWide T400 series, with inline press connection and bidirectional control links if needed. On-the-fly size changes in seconds and production of fully variable book thicknesses are possible. SigmaLine can use a choice of Muller’s perfect binding units for different sizes, needs and capacities: Pantera (hotmelt or PUR), Vareo (with inline Infinitrim three-knife trimmer), or Alegro Digital.
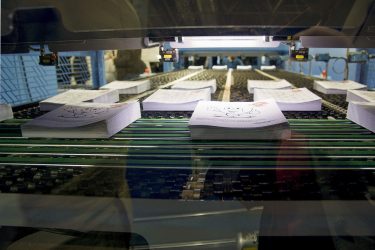
Muller Martini introduced its first SigmaLine system for binding digitally printed books at drupa 2000
Two years ago, Muller bought the book binding lines of German company Kolbus, formerly a major rival in the high-end digital sector. The Kolbus Bookjet KM 200 digital book line is also still sold and supported, offering inline or nearline operations with zero makeready times and on-the-fly size changes at up to 5000 books per hour.
Thread sewing is supported by Muller’s Ventura MC Digital unit, handling up to 9600 digitally printed signatures per hour. Hard cover book blocks, whether sewn or glued, can be bound and cased-in by the Diamant MC digital unit, with variable-thickness rounding and backing. There are two digital-friendly saddle-stitching systems too: Presto II, for up to 9000 cycles per hour, and Primera MC, capable of up to 14,000 cycles per hour.
Hunkeler, which is based in the same Swiss village as Muller Martini, has built up a strong position in web feed and inline/nearline finishing for digital presses. It has a high profile in the industry thanks to its series of Innovation Days every other year (see the February 2019 issue for a report from the last event), essentially an exhibition to show off its integration to third-party systems, especially web-fed digital presses.
At drupa 2012 Hunkeler started offering book signature systems, to feed third party glue binders such as Muller Martini’s Vareo. Its Flyfolder line takes sheets and folds them into signatures, with automatic change over between 4-page and 6-page signatures of different page sizes on the fly. Input can be a roll unwinder, sheeter and dynamic perforator. Speed is up to 128m/min.
For higher throughput, the higher speed Hunkeler Book Block Line can run at up to 200m/min, enough for the fastest digital press, inline if needed, but without on-the-fly signature size changes. The RS8 continuous splicing feeder introduced last year can feed rolls into either the press or a nearline system for uninterrupted operation.
Signatures from both the Flyfolder or the Book Block Line can be assembled into blocks via the SD7 II star wheel stacker, which supports upper and lower paths to allow faster throughput to match fast press speeds, if needed. Temporary spot gluing is used to stabilise the blocks for handling.
Duplo’s range of PUR binders includes the PFI Bind 6000 PUR and Duo, along with the PFI Bind 2100 PUR. The first two are suited to both digital and litho work for up to 300 books per hour. The Duo model can switch between PUR and EVA as needed. The 2100 PUR features a closed tank and patented recirculation to save on glue usage and to cut cleaning and maintenance requirements.
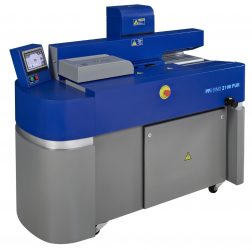
Duplo’s range of PUR binders includes the PFI Bind
2100 PUR
UK-based Morgana now operates as the offline/nearline specialist manufacturer within the Plockmatic Group. Its four Digibook PUR binders cover the speed range from 100 to 450 books per hour. All feature hermetically sealed PUR application systems for spine and side gluing, with automatic glue cut-off, plus automatic cleaning and sealing of the glue head to cut wastage. The fastest 300 XL Pro and 450 models also have spine milling and notching tools for greater glue penetration, which can be retracted to allow for thread binding.
Perfect Bindery Solutions (PBS), established 15 years ago in Oxfordshire by Steve Giddins, doesn’t make machines but imports various products that can be integrated into complete digital binding lines. Central to this is the Risetec automated perfect binding line, with a choice of one, four or seven clamps and the option to run with a Risetec or other make of three-knife trimmer downstream. Alternatively, PBS can supply an IML automated binding line to combine perfect binding, backlining/end-papering and three-knife trimming with variable sizes on the fly at 1250 books per hour with the four-clamp model. For one-offs and short runs there’s also the semi-automatic single-clamp IML BR3-PUR with PUR application for spines plus side hotmelt for manually-applied cases.
PBS also offers thread sewing through the Smyth range. These can run nearline or inline to a binder, with various levels of automation and speed, all able to handle really large books if needed, with spines up to 510 or 520mm long. Smyth’s Digitaline combines buckle folding, collecting into signatures for cross-folding, then thread sewing, while the Digitaline Plus is a hybrid system able to mix digital and litho printed sheets up to 500 x 700mm (and optionally 1000 x 700mm). It can also collect and fold only and eject to a conveyor for separate wire saddle stitching.
Ashgate is a supplier that specialises in very short run but professionally finished books, especially through its distributorship of the Finnish Maping range of Fastbind products. Its entry level is the Fastbind Pureva XT EVA and PUR perfect binder, starting at under £10,000 which means that even small printshops could get into PUR. If you don’t need PUR, the Elite hotmelt-only range offers great flexibility to make hard or soft cover books as well as ‘Manager’ covers, tear-off pads and strip binding.
Inline perfect binders for sheet-fed digital presses are comparatively rare, but can suit mid-volume book specialists. Konica Minolta developed its own inline perfect binder which is offered on mid to high volume Accurio Press models. CP Bourg offers modular inline configurations for most of the other makers: Canon ImagePress and Océ VarioPrint models, plus sheet-fed HP Indigos, Kodak NexPress/Nexfinity, Ricoh Pro C series and most of the Xerox range. These can be configured with the user’s choice from the CP Bourg range of hotmelt or PUR binders, which can all also run as nearline/standalone models with Bourg’s sheet feeders.
Hunkeler also offers a de-stacker to aid later feeding of a third-party perfect binder. Another option is a diverter that allows folding sections to be sent down another path to an inline saddle-stitcher. The UK-built Ibis Smart-binder is recommended; Friedheim supplies this to UK customers.
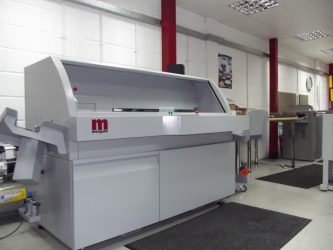
Morgana’s four Digibook PUR binders cover speeds from 100 to 450 books per hour
Tecnau, distributed by IFS in the UK, competes with Hunkeler in paper handling and inline/nearline finishing for digital web presses up to 520mm wide. It offers several ‘on-demand book’ configurations, including the Libra One line that can take rolls and cut, fold and gather 12- or 18-page signatures in variable numbers then pre-glue them into book blocks before being sent to a third-party perfect binder. The ability to produce a final signature of eight or 12 pages means each book can have a different page count on-the-fly; 2D barcodes are used for data integrity. The Libra One CS variant does the same for output from sheet-fed digital presses. Libra 800 adds a hotmelt or perfect binding unit to complete up to 800 books per hour. There are also inline or nearline signature folding and saddle-stitching configurations.
IFS is also distributor for Japanese finishing manufacturer Horizon, which offers book systems at several levels. Its Smart Binding line prepares book blocks from a roll by pairing an unwinder and rotary cutter in-line to an intelligent digital folding machine. Complete book blocks are manually presented to a perfect binder and trimmed on an in-line three-knife trimmer. It can take setup data from the press controller via Horizon’s pXnet bindery workflow system, with barcodes used to set up the perfect binder