In recent weeks we’ve heard from people across the print industry about how the current crisis has affected them and what the ‘New Normal’ might look like. In this article Digital Printer spoke to Plockmatic, Duplo, Friedheim and IFS to investigate how the Coronavirus is changing finishing.
One of the most important questions that needs answering is how will working practices change across the industry. When asked this question Ray Hillhouse, vice president of sales and marketing at Plockmatic Group, immediately brings up remote working and social distancing.
‘I think this depends on the government advice as it emerges and evolves,’ Mr Hillhouse explained. ‘With work that can be done entirely from home, remote working may become a more permanent feature of everyday life. For some jobs, as long as the productivity remains the same, why wouldn’t we endorse this as a policy?
‘However, for other jobs we need to get much more back to the way we did things before the virus. As an example, we assemble machines in our Milton Keynes factory. We can’t afford to just double the size of the floorspace because our workers need to be further apart when assembling – that’s impossible. So I do think there will be short term measures we will need to enforce – but longer term, maybe once we have vaccines in place for this virus or others that may come – we need to get back to what we used to think was ‘normal.’’
Eric Keane, managing director at IFS, focused more on cleaning and hygiene. ‘For the short term we will be introducing more measures that support greater sanitisation with enhanced cleaning procedures,’ he explained. ‘Some of these may well become part of everyday practice. Others may be relaxed and then reintroduced if and when required.
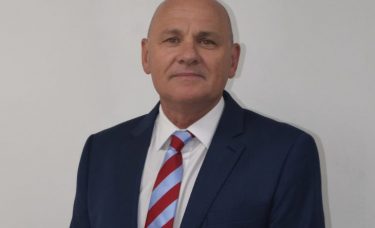
Eric Keane became IFS’ MD toward the end of last year
‘How we demonstrate machines, carry out on-site installations and face-to-face tuition will be challenging, but we are already considering changes in best practice on this to ensure we can be effective but uphold safety and social distancing.’
Martyn Train, managing director at Duplo, split the changes into those impacting sites (social distancing, staggered operating hours) and those affecting the ordering processes, particularly online offerings.
‘The implications of the situation are still unfolding,’ Mr Train said, ‘but organisations need to look at their processes, both in terms of workflow and in terms of mechanical/human processes such as social distancing and staggered shifts.
‘Organisation that bounce back will be the ones that are able to put in place fluid, automated, end-to-end workflow and processes, using the relevant software solutions and automated mechanical solutions to address each step of the process.
‘Flexibility is always key to any survival and for printers, it probably means being able to do more smaller jobs, last minute orders, a wider range of applications, as well as bringing everything in-house. Investing in systems that automate current processes and that open new opportunities and diversify their range of applications, will be key.’
In terms of timelines Mr Train is keen to stress that nothing is ever permanent. ‘Working practices were already evolving; this situation has just massively accelerated a change that was already taking place. Social distancing rules are new, but again, with a clear understanding of processes required in any workplace, they can be addressed for as little impact as can be on the actual work that needs doing.’
This view is slightly at odds with that of Seth Morgan, who handles marketing at Friedheim. Mr Morgan says that, ‘Without the catalyst of a pandemic it was hard to expect any sea change in UK working culture, leaving the efficiencies of working from home (WFH) policies and so on to those bold enough to try, ironically mirroring the UK’s adoption curve for Industry 4.0.
‘Now myriad case studies exist to show that this WFH system can work, and most of us have had an induction to it whether we like it or not. Working remotely poses its own challenges which will probably take a while to figure out on a larger scale. It would be hard to believe anyone has managed this transition so seamlessly it’s caused no gripes, but the technology exists that it certainly can be done with many obstacles already solved.’
Events and product launches
With so many industry events being postponed or suspended, did our four heavyweights think that there would be an impact on the development and release of new technologies or would virtual alternatives suffice?
‘New products are the lifeblood of this industry and we will continue to invest in their launch and development,’ Mr Hillhouse insists. ‘Some of the schedules may be reset, for example products we had slated for launch at drupa will now be introduced at Printing United in Atlanta, but these have already had huge investment for three or more years – so we need to get out there and get on with convincing our customers to invest, tough as it may be for some.’
Mr Keane stressed the role that automation would need to play in the future, and how new technology would be needed to accommodate this, ‘Our supplier Horizon has always been at the forefront in the innovation of print finishing solutions with continually reduced touch points, one-person operation and now full levels of automation. In what will become the ‘new normal’ in the wake of the Coronavirus crisis the need to work in production at distance from colleagues will be inevitable. Horizon solutions meet that need.’
Automation and precision were also key factors for Mr Train. ‘Automation has never been more important than it is now, and our ‘load it and leave’ approach to finishing is a case in point. Automation will play a key role in getting UK PSPs back on an even keel due to less people in factories who are able to work at the same time and even shorter run lengths but a higher number of different jobs. The ability to adapt workflows to changing pressure will mean more connectivity from start to finish.’
Similarly Mr Morgan said that Freidheim has seen a clear‘increase in interest for labour saving equipment and automation. ‘The MBO group has just introduced the Post Press alliance, comprising BaumanPerfecta Wohlenberg, Bograma, Herzog+Heymann, Hohner and MBO, all of which are represented in the UK by Friedheim International – now working together to develop new technologies, operating under the banner ‘We Connect’.
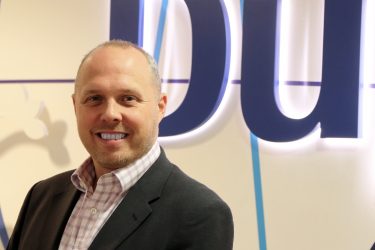
Martyn Train joined Duplo from Xerox in 2019
‘The alliance helps to future proof the groups innovation cycles and crucially keep current and future technologies working in harmony. This all benefits the end user by lowering investment costs and shortening ROI periods.’
Mr Train also suggested that spreading out risk was a key factor. ‘I think print companies need to diversify as much as they can the range of applications they are offering.’ He explained. ‘A digital printer can tap into on demand digital packaging applications for example, broadening their range of customers and adding a new revenue stream. It is about understanding the systems they already own and have and being creative with what else they could produce with it.
‘That is one of the reasons why we are launching in May ‘virtual clinics’ for our Duplo customers. We want to help them achieve more with their existing systems by sharing with them our internal expertise but also answer their questions live to help them truly master their equipment and create new applications for new customers. That has been in the past one of our areas of frustration at Duplo, to see some of our automated systems used for repetitive work when there is so much more that system can do.’
Mr Morgan is far less convinced that the virtual exhibitions are the way of the future. ‘Stakeholders in trade shows such as drupa will likely insist on more robust contingencies in future, and potentially another look at the ‘force majeure’ and cancellation clauses of their contracts and introduce some caveats,’ he said. ‘The scale of fallout from cancellations is yet to be known. Virtual launch platforms are popping up in physical shows’ and this could split the audience. So far there has been a mixed reaction: early launches, sticking to plan launches, and postponed launches. I personally find it odd that drupa has managed to risk their audience, being in the unique position of knowing about the cancellation ahead of everyone else, surely they could have developed a platform to maintain control of the exhibition space, whether physical or virtual.’
Economics
Finally we asked all three companies what their views were on the economic impact this crisis would have on the sector as well as what they thought of the support emanating from Westminster.
‘Clearly some companies will not survive this in their current form and there will be opportunities for consolidation,’ Mr Hillhouse said. ‘I think the level of this will depend on how long the current restrictions are in place. Most companies have some reserves to fall back on – but they won’t last for ever.’
Mr Keane agreed, ‘Any market change will prompt movement of some kind and this may be an opportunity for business with synergies to align. This could be through mergers and acquisitions but also partnerships.’
When it came to the Government, Mr Train was keen to stress the importance of trade associations. ‘The IPIA and BPIF have been instrumental in getting the print industries’ voice heard at BEIS,’ he said. ‘The furlough scheme and the added flexibility spearheaded by the IPIA means that many printers will still be able to get back up and running. However, even more flexibility is needed, especially with the closing of the scheme. Companies must be allowed to gradually ease back into becoming 100% operational. Also, companies will need help with investment in technology. Many PSPs won’t have the ability or cash flow to be able to buy into online printing or automation – to ensure the industry survives automation needs to be incentivised at the government level.’
Mr Hillhouse said that the programme most applicable to him was the Job Retention Scheme, ‘We’ve used this to protect our cashflow and staff the best we can. I think now it’s up and running we’re satisfied with it – but it did give us a couple of weeks of real concern during its implementation.’
For his part Mr Keane said he was able to access the scheme ‘very easily,’ and that IFS received the first payment ‘within a week.’ He added ‘Similarly we have taken advantage of the VAT holiday. We also made a successful application with our bank for the Coronavirus Business Interruption loan, supported by detailed budgets, forecast and a meaningful narrative and received the approval within three days. My feeling is that the Government is very engaged with doing whatever to help business through this unprecedented time.
He did suggest that perhaps slightly more could be done, finishing with, ‘A government campaign to promote the power of print, could perhaps be beneficial. Already some support has been thrown behind newspapers with the placement of adverts. Maybe we could work together to allow reopening businesses to create new promotional print funded by the government? There are very many innovative print businesses in the UK and entrepreneurial owners, they will for sure ‘get-it’ and make headway in what will be a very challenging marketplace.’